Risk Assessment: A Fundamental Part of Labels and Overall Product Safety
Product risk assessments. Product warnings (safety labels and signs). Product manuals and instructions. Each of these three items are key liability prevention documents. But, when it comes to product safety, they don’t operate on their own. That’s because they make up one, intertwined component in a comprehensive product safety strategy; looking at them separately could be detrimental to the safety of the product user and to the liability risk of the manufacturer.
“I always think of it as a braided rope. If you pull these liability prevention documents together, and if they’re intertwined with each other, they’re a stronger set of documents than if they’re looked at separately,” says Clarion Safety’s head of standards compliance, Angela Lambert.
Risk assessment is the foundational element from both a product design and safety standpoint. It’s not possible to control a risk through design, or provide safeguards or warnings unless you first assess it. In this article, we’ll focus on risk assessment and how it relates to machinery safety for OEMs and product safety labels. (We have a companion piece in the workplace safety area of our safety resources that explore risk assessment from that standpoint.)
What is Risk Assessment?
Risk assessment is a tool that manufacturers can use to identify possible hazards and provide a basis for considerations for mitigating or controlling risks. A thorough risk assessment identifies hazards, estimates the severity of injury presented by each hazard, and estimates the probability of the injury’s occurrence. Then, for risks considered “unacceptable” due to applicable laws, regulations, standards, or public opinion, control measures should be applied to reduce risk.
Download Our Free Risk Assessment Info Sheet
Access a starting point for your task-based risk assessments with our ANSI and ISO standards-trained experts.
Get Started Today!
Why is Risk Assessment So Critical for Product Safety?
A thorough risk assessment will identify potential risks and control actions related to them to protect those who interact with your product during its anticipated lifecycle. It’s important to have a complete understanding of the risk assessment process, why it’s needed, and when it’s needed in order to understand your requirements and the safety and liability impact.
For product manufacturers, you must identify potential hazards and then determine if they need to be designed out, guarded, or warned about. From a legal perspective, you must also define what hazards are “reasonably foreseeable” and “reasonable” ways to mitigate risks associated with hazards that cannot be designed out. This is where risk assessment comes into play.
In today’s world, a product is expected to be designed with safety in mind. The risk assessment process helps you to accomplish this task. At its most basic level, risk assessment involves considering the probability and severity of outcomes that can result from potentially hazardous situations. After identifying the potential hazards related to your product at every point in its lifecycle, you then consider various strategies to either eliminate or reduce the risk of people interacting with these hazards.
What is the Risk Assessment Process for Manufacturers?
The best practice risk assessment standards from ANSI and ISO that exist today give you a process to use to quantify and reduce risks. Using these standards as the basis for a formalized risk assessment process will not only help you to develop better safety labels and a safer product, but it will also provide you with documentation that will help you to show the world that you are a safety-conscious company who uses the latest standards-based technology to reduce risks. This will be highly important should you be involved in product liability litigation down the road.
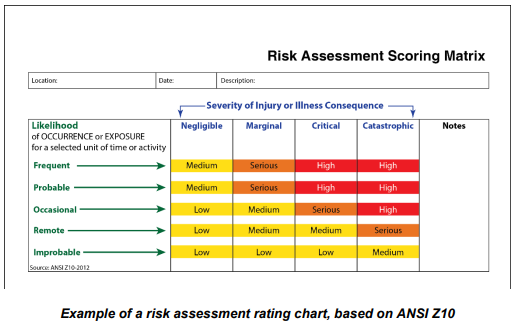
While risk assessment processes vary, the typical process is:
- Identify hazards
- Assess risk
- Reduce risk
- Document results
- Reassess the risk
The hierarchy of controls, used within the risk assessment process, is a guide in implementing hazard control measures beginning with the most effective measures down to less effective ones, and often uses a combination of all. These measures include guards, labels, PPE, instructions, and training.
Avoiding Common Risk Assessment Mistakes
What are some pitfalls to avoid in your risk assessment process? We often see a few common pain points or struggle areas with clients performing risk assessments. These include:
- Using outdated risk assessment methods, instead of current hazard-based and standards-based assessments
- Risk assessments being done by a single person rather than a team
- Risk assessment done ‘for form’ and then filed away without any action taken
The bottom line: to effectively identify, mitigate and communicate about risks, assessments need to be taken seriously, and viewed as an ongoing process to improve safety.
We’re Here to Help
At Clarion Safety, we’re committed to being your partner in product safety, in line with your specific needs. In addition to our safety and education resources, our trusted OEM solutions for machine builders include risk assessment solutions throughout your product’s lifecycle. We offer machinery risk assessments for OEMS, machinery risk assessments for workplaces, machine manual audits, and label/sign assessment services.