With stepped-up OSHA enforcement and disproportionally large personal injury settlements now commonplace, it’s no wonder that employers face more questions than ever related to the safety of their machinery. Clarion Safety’s expert team can provide clear answers and help solve your OSHA machine safeguarding issues. We provide safety interlock and design review services and can upgrade your machines, as your full-service partner in increasing safety.
Functional Safety Reviews & Regulatory Verification
In the U.S., functional safety (such as ‘interlocks’ and safety rated devices) and control reliability are essential concepts for increasing safety and in fulfilling OSHA’s “Minor Servicing Exception” for lockout/tagout (LOTO). Internationally, compliance implications with ISO/IEC standards and CE marking for machinery also exist.
With our safety verification and validation services, our certified safety engineers at Machine Safety Specialists (MSS) apply our specialized knowledge and real-world experience to your application, verifying compliance with regulatory requirements and validating machine safety functions. Conducted in the form of a functional safety review, our engineers conduct control reliability design reviews with clear guidance on meeting standards – often based on your drawings and Bills of Materials. Our Control Reliability Design Reviews and SISTEMA Analysis can be performed remotely and off-site, and are conducted by our experienced, TÜV certified safety engineers. Our Control Reliability/Functional Safety Design Review service includes an engineering review of system drawings and technical information to see if a system is control reliable in accordance with OSHA, ANSI, and NFPA standards. Depending on the application, control reliability may also be satisfied by safety functions meeting or exceeding Category 3, Performance Level (PLd) as defined by ISO 13849 and ANSI B11.26.
Our SISTEMA Analysis with Report provides a quantitative analysis of the machine’s functional safety system, and calculations are based on safety-related devices shown in customer supplied documentation. These functional safety services are among our most popular options, but our team at MSS also offers additional solutions to meet your specific needs, including stop-time measurement services, validation plans, and validation testing reports.
Machine Safety Validation Review Process
Control Reliability Safety System Design
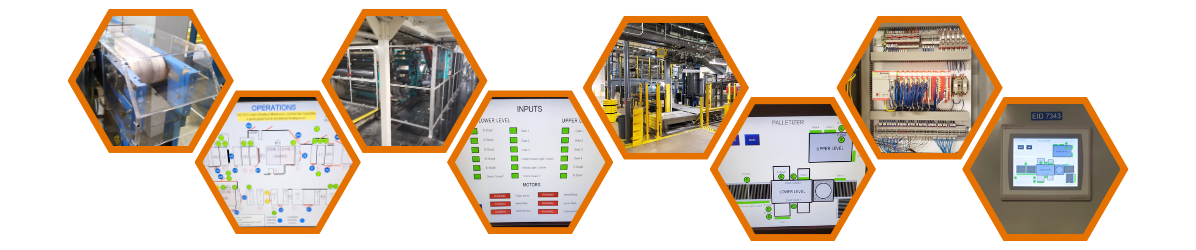
After an initial system review is performed, you may be ready to take the next step in designing or upgrading your machine's electrical safety system to meet the safety standards for control reliability and alternative protection methods. Traditional programmable logic controllers (PLCs) have limitations when it comes to safety. Our control reliable safety system design and integration services through Arrow Industrial Solutions pick up where MSS leaves off; we ensure your machinery meets the standards set forth by OSHA, ANSI, ISO and include the recommendations from any previous functional safety reviews. Generally, we come on-site to personally inspect your machine after reviewing any prior risk assessments and reports. This framework helps us design systems that:
- We will design a control system hardware solution based on your process, applicable standards, preferred equipment suppliers, and document formats.
- Our team will design your machinery control system to optimize safety, reliability, efficiency and control integration.
- Instrumentation is specified to meet the necessary control reliable category determined in the risk assessment to provide a compliant solution. We have complete Safety Control capabilities and can provide all components, devices and control panels for a turnkey solution.
- Arrow's design team coordinates with your production teams to seamlessly integrate these control systems to minimize production downtime and interference with operations.
FAQs About Our Functional Safety & Design Services
How can interlocked guards be integrated with existing machinery?
Integration of interlocking guards with existing machinery can be achieved through the following steps:
1. Conduct a thorough risk assessment to identify hazardous areas and determine the appropriate placement of guards.
2. Select interlocking devices that are compatible with the machinery and suitable for the identified hazards.
3. Ensure proper installation and alignment of interlocked guards with the machinery.
4. Connect interlocking devices to the control system of the machinery, establishing the necessary communication for activation and deactivation.
Are interlocked guards mandatory for regulatory compliance?
The requirement for interlocked guards depends on the specific industry and applicable regulations. However, in many cases, interlocked guards are indeed mandatory for regulatory compliance, including OSHA standards for machine guarding in the United States (29 CFR 1910.212) and ISO 14119, which provides guidance on interlocking devices associated with guards, and Industry-specific standards such as ANSI/PMMI B155.1 for packaging machinery safety.
Can interlocked guards be retrofitted to older machinery?
Yes, interlocking guards can often be retrofitted to older machinery to enhance safety. The process may involve:
- Conducting a risk assessment to identify the necessary guard modifications or additions.
- Identifying suitable interlocking devices that can be integrated with the existing machinery.
- Ensuring compatibility between the interlocking devices and the machinery's control system.
- Adhering to relevant industry standards and guidelines during the retrofitting process.